The Importance of Equipment Qualification in the Nuclear Industry Supply Chain
1. Nuclear Renaissance and the EQ Imperative
The global nuclear industry stands at a pivotal juncture, characterised by escalating decarbonisation imperatives and advancing reactor technologies. Within the UK context, government commitments to 24GW of nuclear capacity by 2050 underpin monumental projects: Rolls-Royce SMR aims to deploy factory built 470MW units from the mid-2030s, while Sizewell C’s twin EPR reactors (3.2GWe) promise low-carbon baseload power for six million homes. Yet these projects face historical challenges, such as cost overruns, schedule delays, and supply chain constraints, that threaten their realisation. At the heart of mitigating these challenges lies equipment qualification (EQ), a systematic process providing documented evidence that electrical, instrumentation, control, and mechanical equipment will reliably perform safety functions under all operational and accident conditions.
Beyond its safety mandate, EQ profoundly influences supply chain dynamics. The nuclear sector’s stringent technical requirements traditionally created high entry barriers, limiting supplier diversity and inflating costs. However, modern EQ methodologies can paradoxically broaden supply chain participation while enhancing quality assurance. Through examination of EQ frameworks, regulatory standards, and UK project applications, we establish how strategic EQ management transforms qualification from a compliance exercise into a competitive enabler for technology providers, component manufacturers, and engineering services alike.
2. Fundamentals of Nuclear Equipment Qualification
2.1 Definition and Safety Rationale of EQ
Equipment qualification (EQ) constitutes a lifecycle assurance process demonstrating that safety-related equipment can withstand specified environmental stresses (thermal, seismic, radiological) while maintaining functional performance throughout its service life. Unlike conventional quality control, EQ specifically addresses abnormal and accident conditions, such as loss-of-coolant events or seismic incidents, where equipment failure could compromise fundamental safety functions. The IAEA explicitly mandates EQ to "confirm reliable performance of safety functions... to avoid vulnerability due to common cause failure". The purpose of EQ is to provide confidence that the equipment will operate as required during normal operation, transient conditions, and accident scenarios, thereby contributing to the overall safety and reliability of nuclear power plants.
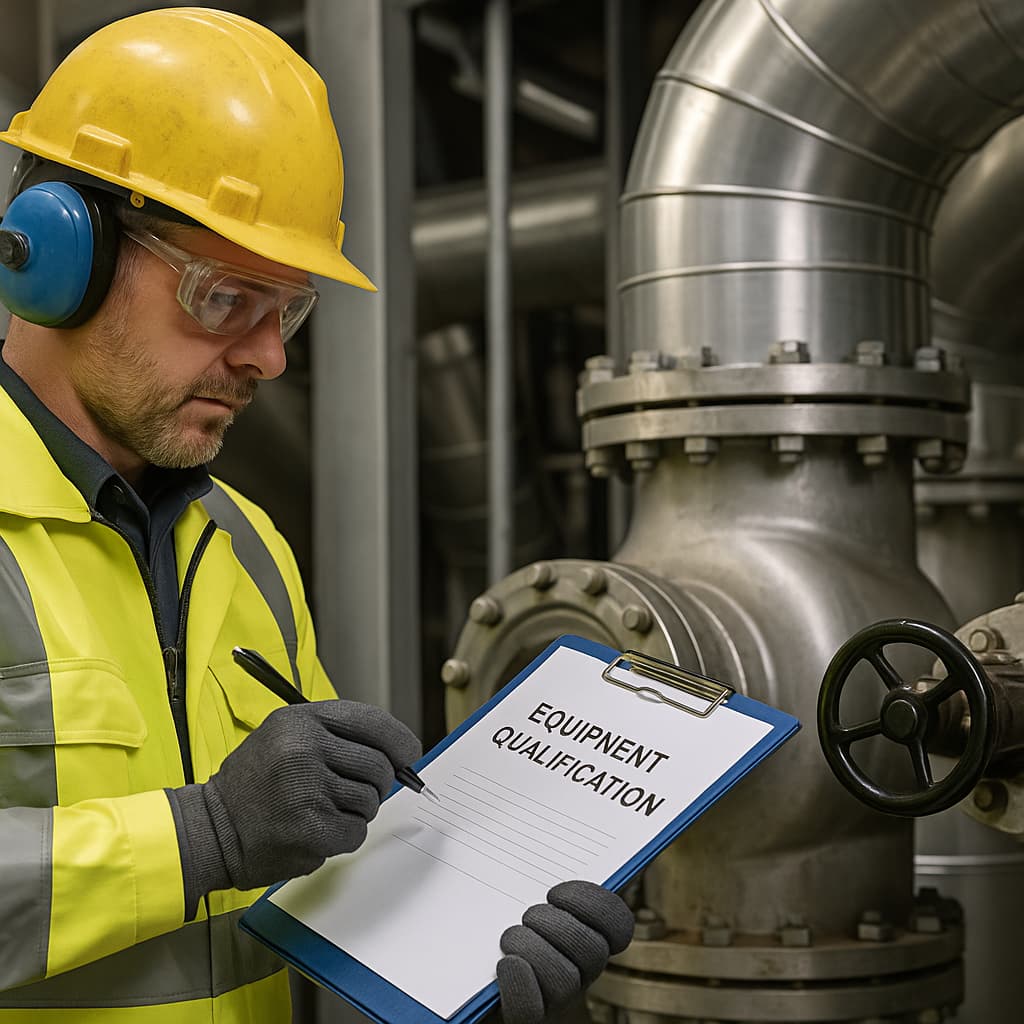
2.2 EQ Scope and Categorisation
Nuclear EQ encompasses:
- Electrical Equipment: e.g., switchgear, motors, inverters, cables
- Instrumentation & Control (I&C): Sensors, control and protection systems, actuators
- Active Mechanical Components: e.g., Pumps, valves, drives, etc.
- Associated Items: e.g., Pumps, valves, motor, drives, etc.
The qualification must address all relevant environmental and operational stressors, such as: temperature and humidity extremes, radiation exposure, seismic events and vibration, pressure and chemical exposure, and electromagnetic interference. Passive mechanical components (e.g., piping, vessels) generally fall outside EQ scope, as their safety performance is assured through design codes and in-service inspection. Crucially, EQ applicability extends beyond new builds to include ageing management and lifetime extension programmes for existing fleets, known as "progressive qualification".
3. Codes and Standards Frameworks, Regulatory Landscape
Nuclear EQ is governed by a framework of international and national standards. The IAEA’s Safety Requirements (SSR-2/1 Rev.1) mandate that “Items important to safety…shall be designed in accordance with the relevant national and international codes and standards.”. In practice this means suppliers must adopt recognised nuclear standards when qualifying equipment. Key standards bodies include the International Electrotechnical Commission (IEC), the IEEE Nuclear Power Engineering Committee (NPEC) and AFCEN. For example:
- The IEC/IEEE 60780-323 standard (electrical equipment important to safety – qualification) now harmonises electrical EQ requirements globally.
- The IEC/IEEE 60980-344 standard covers seismic qualification of safety-related equipment.
- Other IEC standards cover environmental testing, insulation, cabling, instrumentation (SC45A, SC45B, TC65).
- RCC-E and RCC-M: These are French standards (RCC stands for "Règles de Conception et de Construction") developed by AFCEN, a French organisation specialising in nuclear standards. RCC-E covers electrical equipment, while RCC-M covers mechanical components.
In short, the UK nuclear supply chain typically applies the IEC side (supported by IAEA Safety Guides). Rolls-Royce’s SMR design, for instance, uses international codes vetted by ONR, while the EPR at Hinkley/Sizewell uses French standards RCC-M and RCC-E with ONR’s oversight. Suppliers must be familiar with these standards (and any UK-specific guides or ONR Safety Assessment Principles) to ensure their qualification meets regulatory expectations.
4. The Equipment Qualification Process: Lifecycle Stages
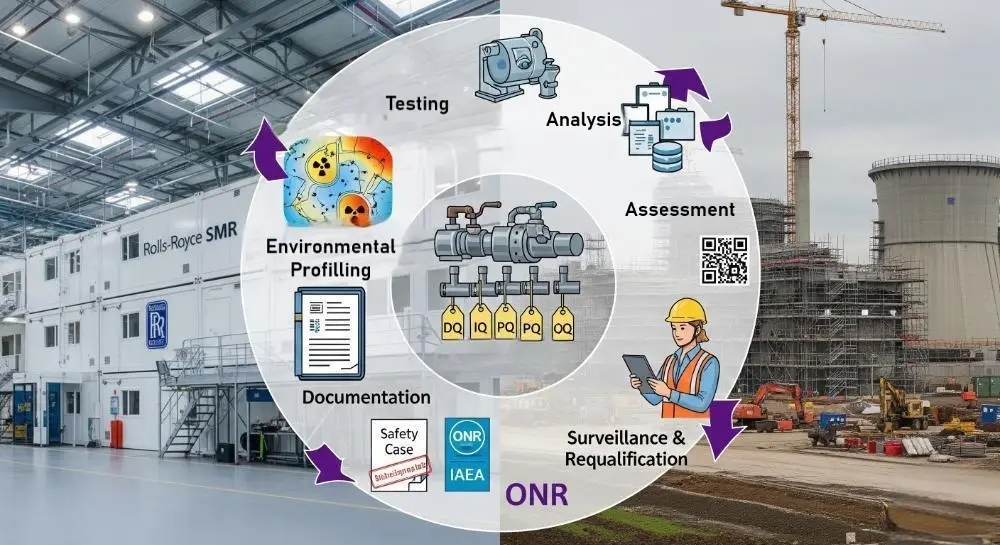
4.1 Design Input Phase
EQ commences at conceptual design through environmental profiling to identify all safety functions and service conditions, by defining temperature, pressure, radiation, humidity, and seismic conditions for each location. This means deriving requirements from system safety analysis (e.g. reactor shutdown, core cooling) and normal/accident parameters. Each piece of equipment gets a Design Data Sheet listing its Qualified Life, mission time, load profiles, and environments. For Rolls-Royce SMRs, factory-based module construction necessitates "design-for-qualification" approaches where equipment representation (e.g., boundary conditions) is meticulously planned for future testing efficiency.
4.2 Qualification Methodology Selection
Once the design inputs and requirements have been identified, the next step is to select and implement appropriate qualification methods. These methods are designed to demonstrate that the equipment meets the required performance criteria under specified conditions.
- Environmental Testing: This involves subjecting the equipment to simulated environmental conditions to assess its performance. Tests include thermal cycling to evaluate performance across temperature extremes, radiation exposure tests to determine the effects of radiation on materials and components, and seismic tests to simulate earthquake conditions. For example, a seismic test on a control rod drive mechanism involves using a shake table to apply forces equivalent to those expected during a seismic event.
- Operational Testing: This method evaluates the equipment's performance during normal operation and under transient conditions. It includes functional tests to ensure that the equipment operates as intended, endurance tests to assess long-term performance, and dynamic tests to evaluate response to sudden changes in operating conditions. For instance, an endurance test on a pump in a nuclear plant involves running the pump continuously for an extended period to ensure it maintains its performance without failure.
- Accelerated Ageing: This technique is used to simulate the long-term effects of environmental conditions on equipment. By applying accelerated ageing factors, such as increased temperature or radiation dose rates, the equipment's performance over its expected lifetime can be predicted. For example, an electronic component may be tested at elevated temperatures to simulate the ageing effects that would occur over several years of normal operation.
- Analytical Methods: These involve the use of mathematical models and simulations to predict the performance of equipment. Analytical methods can complement physical testing by providing insights into the equipment's behaviour under various conditions. For example, finite element analysis can be used to predict the stress distribution in a containment vessel under different loading conditions.
- Combination of Methods: In practice, a combination of environmental, operational, accelerated ageing, and analytical methods is often used to provide a comprehensive assessment of the equipment's qualification. Another example is combining seismic simulation with electromagnetic compatibility (EMC) testing to reduce rework. This approach ensures that all potential failure modes are identified and addressed.
4.3 Implementation and Documentation
Qualification programmes proceed through interconnected stages:
- Design Qualification (DQ): Verifying equipment design meets environmental specifications
- Installation Qualification (IQ): Confirming proper installation against manufacturer criteria
- Operational Qualification (OQ): Testing functionality under operational envelopes
- Performance Qualification (PQ): Validating performance under accident scenarios
Among these, nuclear PQ requires ageing simulation – artificially ageing samples to demonstrate endurance throughout qualified life. Documentation must comprehensively address equipment configuration, test conditions, acceptance criteria, and deviations.
4.4 Ongoing Surveillance and Re-qualification
Post-installation, EQ mandates condition monitoring and periodic re-qualification to address age-related degradation mechanisms. Progressive qualification programmes, such as those for life extension beyond 40 years, employ sampled equipment from sites to establish ongoing qualification viability.
5. Best Practices for Equipment Qualification in the UK Nuclear Industry
Effective equipment qualification (EQ) within the UK nuclear industry necessitates its holistic integration throughout project design and construction phases. This approach ensures components are conceived, validated, and installed with explicit consideration of their intended operational environment, thereby maximising inherent safety and reliability. During the design phase, EQ requirements must be embedded within specifications to guarantee equipment resilience against specific environmental and operational demands, facilitating early issue identification. Construction phase coordination is equally critical, ensuring correct installation and that modifications preserve qualification integrity through activities like concurrent in-house verification.
Furthermore, robust collaboration with suppliers constitutes a critical best practice, given their pivotal role in meeting the sector's stringent safety standards. This entails meticulous supplier selection based on proven nuclear qualification expertise and adherence to recognised standards like IEEE 323 and IEC 60780. Collaboration extends to joint testing and verification activities, such as environmental and accelerated aging tests conducted in partnership, alongside rigorous supplier quality assurance systems subject to regular audits. Knowledge sharing between project teams and suppliers underpins continuous process improvement.
Finally, maintaining equipment qualification demands continuous monitoring and improvement throughout the operational lifecycle. Implementing advanced condition monitoring techniques provides real-time health assessments and enables proactive maintenance. Regular requalification, scheduled according to equipment criticality and performance data, addresses potential degradation. Feedback loops from monitoring and maintenance inform the refinement of protocols and techniques, while ongoing regulatory engagement ensures alignment with evolving standards and expectations.
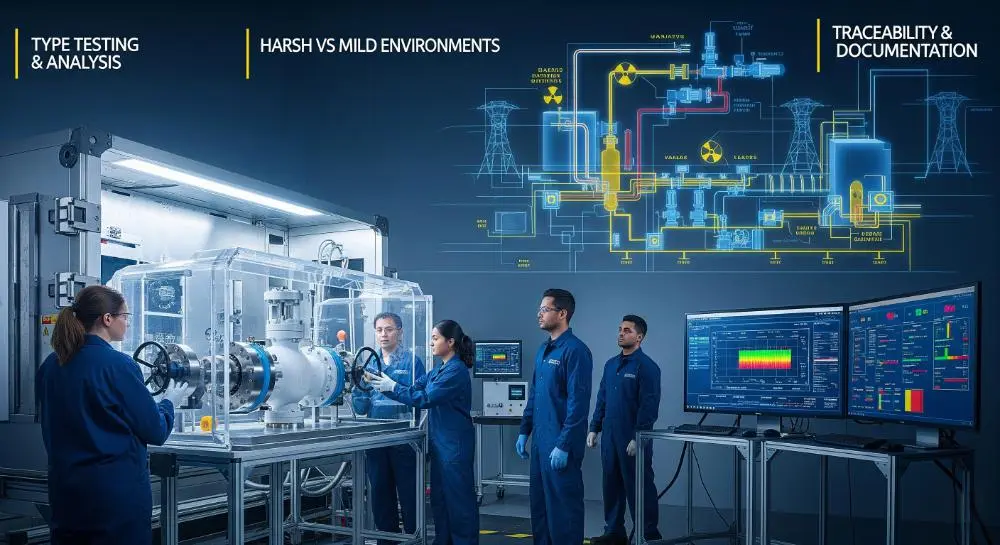
6. Future Trends and Innovations in Equipment Qualification
6.1 Technological Advancements
The future trajectory of equipment qualification (EQ) within the nuclear industry will be profoundly shaped by ongoing technological innovation. These advancements promise to significantly enhance the efficiency, accuracy, and overall reliability of qualification processes, thereby ensuring nuclear equipment consistently adheres to the most stringent safety and performance standards critical for nuclear operations.
Key developments include the proliferation of sophisticated simulation and modelling techniques, such as finite element analysis (FEA) and computational fluid dynamics (CFD), enabling highly accurate prediction of equipment behaviour under diverse stressors like thermal cycling, radiation, and seismic events. This reduces reliance on extensive physical testing while improving failure mode identification and design optimization. Concurrently, the adoption of digital twins facilitates real-time performance monitoring and predictive maintenance based on historical and operational data, supporting continuous qualification throughout an asset's lifecycle. Furthermore, artificial intelligence (AI) and machine learning (ML) algorithms are increasingly employed to analyse large datasets from testing and monitoring, enabling early anomaly detection and predictive maintenance interventions.
Parallel advancements in material science are yielding novel materials, such as advanced ceramic composites and radiation-resistant alloys, with superior resistance to harsh environmental conditions. This inherent resilience reduces qualification burdens for critical components like reactor vessels and fuel assemblies. Complementing this, enhanced non-destructive testing (NDT) techniques—including advanced ultrasonic, eddy current, and radiographic methods—provide more precise and comprehensive condition assessments, enabling earlier defect detection and more effective maintenance planning to sustain equipment qualification and operational safety.
6.2 Regulatory Developments
Regulatory developments will fundamentally influence the future of equipment qualification (EQ) in the nuclear industry, adapting requirements to uphold paramount safety and reliability standards as the sector evolves. A significant trend involves the harmonisation of national and international standards, driven by bodies like the IAEA, to reduce complexity and cost, particularly for multinational endeavours. Concurrently, regulatory approaches are increasingly adopting risk-informed principles, where the rigor of qualification is proportionate to the safety and environmental consequences of potential equipment failure, thereby optimising resource allocation towards critical components.
Further evolution entails enhanced regulatory flexibility to accommodate technological innovation, potentially allowing validated advanced simulations within qualification processes. Imperatively, the digitalisation of facilities necessitates the integration of robust cybersecurity assessments and countermeasures into EQ frameworks to mitigate evolving cyber threats. Finally, as decommissioning and waste management gain prominence, regulatory standards will specifically address the qualification of equipment for these complex, long-term activities, ensuring safe and reliable performance under unique operational conditions.
6.3 Industry Collaboration
Industry collaboration will constitute a critical catalyst for innovation and enhanced efficacy in nuclear equipment qualification (EQ). By fostering synergistic partnerships among stakeholders, knowledge, resources, and best practices can be systematically shared, leading to demonstrably more effective and efficient qualification methodologies. This cooperative paradigm is essential for addressing the sector's complex challenges.
Key collaborative mechanisms include joint research and development initiatives uniting industry, academia, and regulators to advance novel materials, simulation tools, and non-destructive testing techniques, as exemplified by potential partnerships like the UK's Nuclear Industry Association and Office for Nuclear Regulation. Furthermore, dedicated knowledge-sharing platforms will provide centralized repositories for qualification data, test results, and lessons learned, facilitating widespread access and continuous improvement. Concurrently, industry-wide standardisation initiatives will develop common protocols, test methods, and documentation formats, significantly reducing qualification complexity and cost while ensuring consistent safety and reliability standards.
Effective implementation will also be driven by structured supplier networks, enabling component manufacturers to share resources and best practices to meet stringent qualification criteria, particularly vital for novel systems like the Rolls-Royce SMR. Finally, international cooperation is imperative, allowing nations with advanced nuclear capabilities to harmonise standards and qualification protocols, thereby promoting a globally efficient and robust EQ framework. This multi-faceted collaborative approach is fundamental to future progress.
7. Conclusions
Equipment qualification is a critical enabler of nuclear safety, reliability, and regulatory compliance. It underpins the confidence that systems and components will perform their safety functions under all anticipated conditions, protecting people, the environment, and investments. The UK nuclear sector, through projects such as Rolls-Royce SMR and Sizewell C, is at the forefront of implementing robust EQ practices, aligned with international standards and tailored to the unique demands of modern nuclear installations.
The trajectory is clear: future nuclear projects will increasingly demand integrated EQ solutions spanning design, testing, and operational surveillance. For technology providers and component manufacturers alike, investing in EQ capabilities today represents not merely risk mitigation, but a powerful catalyst for business growth in the nuclear supply chains of tomorrow.
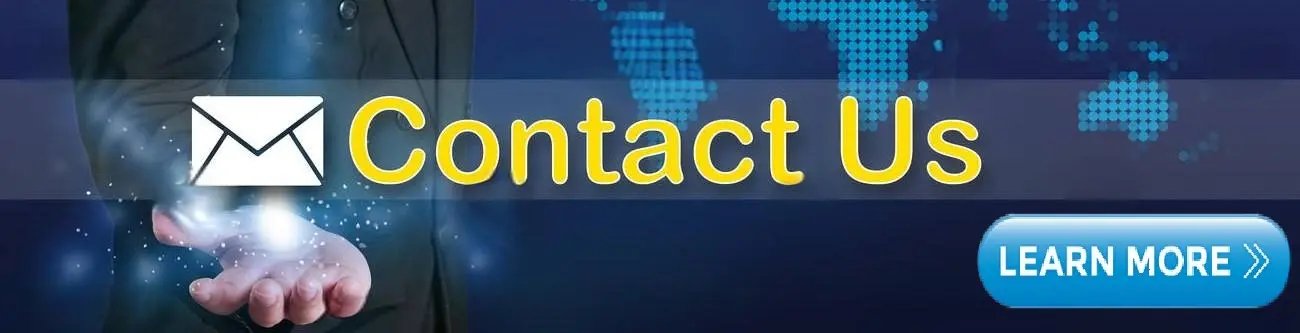
Back to the list